Comme premier article je vais vous parler d'un powermeter , entièrement fait maison et correctement calibrer qui n'as rien a envié au modèle du commerce souvent très couteux !
1.Les prémices !
le première prototype crée , il se basais sur l'utilisation de deux diode 1n4841 qui montée en comparateur de tension , donnais une valeurs précise en fonction de la température appliquée sur une des deux diode , une diode étais la référence et l'autre le capteur , l'avantage étant le faible cout de fabrication , une précision intéressante ! le désavantage était la puissance mesurable faible 1watt maximum ,une surface de mesure trop petite avec beaucoup de réflexion parasite et une inertie thermique importante il fallait 1 ou 2 minute après une mesure pour qu'il revienne a zéro et ça pour des puissance de 300mw !! c'est trop , bcp trop
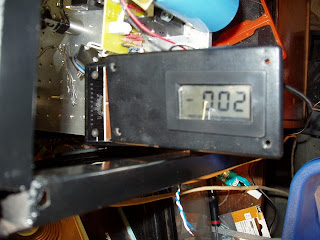 |
vue sur l'afficheur LCD |
 |
Vue interne , admirer la simplicité du montage :) |
|
|
|
| |
| |
2.Amélioration
Une évolution du modèle , en effet il fallait améliorer le capteur , et tant que a faire , lui donner un look
plus pro , donc récupération d'un bout d'alu , montage sur le tour , et tournage , après quelque heure je me retrouve avec ceci ! , une belle pièce en alu et un insert en PVC , insert qui va supporter la diode et un insert en cuivre de 0.5mm d'épaisseur qui serviras a transférer la chaleur reçue a la diode Zener , ainsi que un trou fileter pour fixer le capteur sur un support adéquat !
 |
l'assemblage |
 |
une vue arrière de la tête , avec un emplacement pour l'électronique |
 |
une vue désassemblée du capteur , très simple enfaite :) |
 |
la tête complète | | |
Ceci était le premier prototype , mais comme il ne me convenais pas , et que la diode capteur n'était pas stable (erreur importante entre deux mesure du au stockage de chaleur au capteur ) ,du au fait que la Diode ne tenais pas le watt je fut déçu et j'ai abandonné se projet , l'électronique n'as même pas été finalisée il sera ranger dans le musée souvenir :)
3.Changement de capteur !
après cette échec plutôt découragent , 1ans ses passer avant la suite , d'autre projet s'étant intercaler entre temps :) , j'ai décider de reprendre le projet , j'ai aussi pu constater un effet intéressant dérivé de l'effet pelletier et donc plus communément appeler TEC ( thermo electric cooler ) , et cela grâce aussi a de nombreuse recherche sur le net , au vue d'idée récoltée de schéma , ect ect , j'ai décider d'en faire un moi aussi , mais en améliorant considérablement se que j'ai pu trouver tout en restant dans le simple :), le principe est simple , le tec fonctionne a "l'envers" si on garder une température fixe d'un coter et que de l'autre coter on y applique du froid ou de la chaleur il va génère une tension qui est proportionnelle a la température reçue , et cela avec une rapidité intéressante et une inertie très faible , de plus la céramique utilisée résiste a de très forte puissance laser , on as donc la notre capteur pyroélectrique ou Thermopyles économique ^^
4.usinage du capteur
je me suis inspirer de modèle existant dans le commerce pour la partie esthétique histoire que ça en jette un peu ^^ , et que cela fasse moins bricolage que se que j'ai pu trouver en Diy dans mes recherche !
Après 5heure d'usinage sur mon petit tour on sort ceci !
 |
la tête nue avec ses deux pièce emboitée |
|
| |
|
| |
 |
les deux partie principal avec un TEC de 15*15mm comme capteur |
une fois l'opération de tournage terminée et les cote revérifiée et acceptée , on passe a la partie fraisage , afin de faire les trou de fixation , l'emplacement du DB9 et on va assembler le tout , a noter que la tête intègre le tec de 15*15mm , 10 résistance CMS soudée en série et collée sur le contour du coter capteur (afin d'auto calibrer le powermeter ! ) et de deux ntc (capteur de température) afin de prévoir par la suite si besoin est une stabilisation en température pour compenser les fluctuation a cause des courant d'air éventuelle sur la tête ( étant donner que l'on crée un pont thermique de mesure , la moindre influence de température sur une des deux face va automatiquement génère une tension au borne du TEC et permettre une mesure précise d'un laser dans mon cas , mais peu mesurer toute source de chaleur proche , il faut donc garder cette équilibre donc la partie "radiateur" doit avoir une valeur stable !
après 2heure de fraisage et finition diverse !
 |
l'usinage principal terminer ! |
6.préparation de la "boite"
Alors le capteur c'est bien beau il est tout joli il me plait , mais il va falloir une boite qui va intégré l'alim sur accus , l'électronique de mesure et de compensation , et surtout l'affichage avec si possible une belle sérigraphie (ça fait plus pro ^^ )
Après un petit tour a mon magasin d'électronique favoris , je suis revenus avec a peu prêt tout les composant utile et une belle box :)
 |
la box et la sérigraphie de "test" pour voir ^^ |
| |
|
|
|
|
j'ai passé quelque heure sur un super soft , entièrement gratuits , qui est fait pour réaliser et imprimer toute sorte de face avant et de fond de "galva" très utile pour moi car j'ai du faire ma propre échelle de mesure !!
donc après pas mal d'heure j'ai obtenus se que l'on vois plus haut , ça me parais parfait , reste que je n'ai pas encore finaliser le boitier avec se jolis fond !! vivement la découpeuse cnc de vinyle ^^
7. L'électronique Prototype
on y arrive , le montage de tout ça , la création des pcb diverse au bon fonctionnement de la bête !
Prototypage on teste le schéma sur plaque a essais et on valide les composant et on se base la dessus pour faire un bon schéma et un pcb adéquat
 |
on monte sur protoboard |
 |
l'électronique , rien de compliquer :) |
 |
premier test , wooow ça fonctionne dit donc ! |
 |
on fait un essai de calibration , ça a l'air de coller avec la puissance du laser utiliser :) |
8.L'électronique , finalisation et montage
on repasse encore pas mal d'heure a mettre sur pcb les schéma crée , faire en sorte que tout se petit monde rentre dans se petit boitier que je trouvais déjà trop grand ^^ (comme quoi je vais devoir refaire un autre boitier bientôt ^^ )
on usine aussi la face avant , pour y insérer l'afficheur a aiguille et l'afficheur LCD , et les bouton !
 |
c'est serrer ^^ |
 |
très serrer mais ça rentre :) |
9. Test et conclusion
a cette étape ci on as presque fini , je n'ai pas de photo du montage du capteur , mais il as été assembler un peu avant le boitier :) a noter que sur la surface du capteur j'ai appliquer une peinture noir mat high température pour éviter les reflet et donc absorber un max le rayon , soucis la peinture ne tient pas au delà d'un watt de laser il faudrait étudier la solution pro qui consiste a vaporiser de la vapeur de carbone sous vide !! , petit reproche par contre a l'afficheur LCD il ne fonctionne que avec une source de tension indépendante de la source de tension mesurée , donc il ne sert a rien car je l'ai pas la place pour rentrer une pile de 9volt en plus c'est très dommage ca aurais permis une mesure plus précise , j'attends donc de trouver un lcd qui n'as pas se soucis !!!
 |
le boitier fini , et calibration faite c'est impeccable ! |
 |
une vue avec l'éclairage bleu de l'afficheur ( et on vois bien que le lcd est a l'ouest !) |
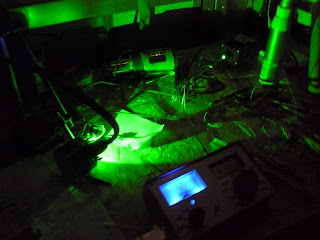 |
une vue de "nuit" laser vert sur le capteur et led bleue a l'afficheur j'aime :) |
pour le boitier en détail ! , il peu mesurer de 10miliwatt a 30watt (le capteur peu tenir 10watt de laser ) les deux afficheur on des sortie réglable indépendante , et donc on peu ajuster au poil :) , il y as une sortie monitor sur mini BNC a l'arrière , pour brancher sur un logger afin de génère des graphique ,niveaux de sortie 0-300mv DC il fonctionne sur deux pile 9V pour crée une alim symétrique , mais fonctionne aussi sur secteur garce a un adaptateur spéciale conçus exprès !
A noter aussi le cable de liaison tête-afficheur , réaliser sur mesure afin d'avoir un câble coax blinder pour le capteur !!
la face avant finie ,je lui trouve un petit aspect "pro" , il reste a faire anodiser le capteur en noir aussi ! et surtout a trouver un afficheur LCD qui répond a mes besoin !!
quelque vue du capteur fini , avec sont support adapter !
10. conclusion !
on peu parfaitement fabriquer cette outil soit même , pour peu que l'on soit patient et que l'on gère un peu d'électronique et mécanique a savoir qu'un ensemble comme celui ci peu vite dépasser les 1000er d'euro !
les résultat obtenus sont TRÈS positif , la mesure est très précise , stable , rapide et le capteur est très sensible on as une grand précision , je pense peu être un jour refaire un capteur plus gros , pour des laser plus puissant a voir !!
(pour toute question , ou demande de schéma , me contacter directement merci :) )